Jean-Marc Peallat—Vi Technology
当用户开始从元器件级上认识到焊膏沉积质量和焊接工艺之间清晰的关系时,3D焊膏检查在测试策略中将扮演越来越重要的角色。
多年来,许多工艺工程师和质量管理者一直对焊膏检查仪(SPI)所带来的效益存在疑问。尽管在SMT的工艺流程中往往伴随着很高的缺陷等级,但很多SMT生产线都不曾真正执行过SPI检测。一些用户质疑其成本效益的分析结果,而另外一些用户则认为SPI,特别是3D SPI,仅仅在新产品导入(NPI)阶段或产品试制期有用,而对于已经成熟的产品工艺是无利可图的。对他们而言,SPI所提供的信息既不会带来相关产品的任何质量提升,也不会把这种提升的需求和SPI设备配置不足挂起钩来。
无论如何,随着当今先进工艺趋向于使用更小的元件,如01005、μBGA或PoP,在SMT生产工艺中使用实时检查显得尤为重要,而且会成为确保质量的标准工序。所以,人们意识到需要重新发掘3D SPI的功能,也认识到仅仅计算体积已不足以确保工艺质量。
焊膏印刷工艺
与其他SMT工艺相比,因为存在着更多的变数,焊膏印刷工艺有着潜在的不稳定性。根据众多公司和大学的研究结果,印刷工艺有着大于60%的可变性。之所以存在这么大的可变性,是因为印刷工艺中包含大量不确定的工艺参数,一般认为这些参数变量的总和接近40个,包括(而不是仅仅局限于)焊膏的种类、配方、环境条件、模板的类型、模板厚度、开孔的宽厚比和面积比、印刷机类型、刮刀、印刷头技术、印刷速度等等。
典型的印刷机性能量化参数有:转移效率(TE)百分率和焊膏沉积的标准差,100%意味着PCB上的焊膏轮廓正好与开孔的计算体积相匹配。有意思的是,一个典型的SMT板的转移效率可以在20~130%之间变化。
尽管矩形开孔的转移效率通常要好于正方形和圆形的开孔,但印刷时它在水平或垂直方向上仍然会存在体积差异。垂直的开孔在有稍大一点的孔容时印刷效果较好,而印刷效果最差的情况出现在直径小于0.012英寸的圆形或正方形的开孔上。要注意的是,转移效率降低时标准差也将增加,同时转移效率的降低也会导致体积重复性的减低。
另一个有趣的现象是,研究显示,对于一个阵列型封装来说,焊膏体积的重要性不如全部阵列焊盘的一致性,即只要所有焊盘上有同等量的焊膏,都将被接受。可如果某些焊盘上的焊膏少于阵列中其它的焊盘,则可能导致不良焊点的出现。
技术观点
同AOI一样,用于SPI的技术在过去十多年里没有太大的进步。现在有两种方法来检查焊膏,一是激光三角法,另一个则基于莫尔(Moiré)技术。下面我们来比较这两种技术,考察它们各自的优缺点。
激光三角法
激光三角法是结合2D图像,通过激光的轨迹差来获得被测物体高度的(见图1和图2)。
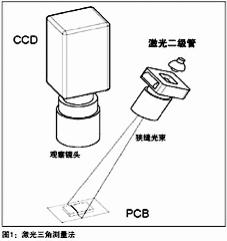
此法的缺点主要是分辨率不够导致较低的精度。此外,使用单个激光源不能计算出容积的准确值。此现象被称为“阴影效应”,源自于系统的几何设计。单一角度的激光源和镜头的组合,可能会在焊膏沉积物的背面产生一个盲点(见图2)。
如图2中焊膏沉积物的方形区域中,在隐藏区域(红色)的焊膏量是不能被计算出来的。圆形孔的测量值误差依形状的不同最高可达48%。