图8:测试方法
值得注意的是,在同一块电路板上铜厚的差异是显著的,最大可以达到50微米,但是在比较前/后铜厚变化的时候会将此因素考虑在内。图9显示的就是一个典型的实验样本。
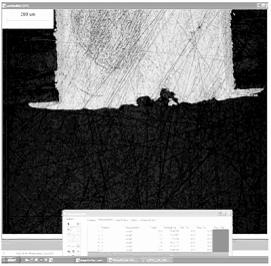
图9:SPTH(波峰形式—Chip+Main,焊料合金SAC305,传送带速度1.5尺/分钟,电路板供应商A)
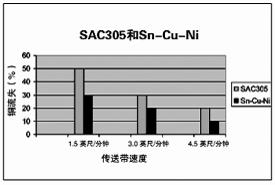
图10:不同传送带速度下的铜流失
在4个因子中间,波峰形式对铜腐蚀的影响是最大的。实验中用了三种波峰形式:单个宽的扰流波,单个λ型平滑波,和以上两种组合成的双 波峰。图10为在两种合金三种导轨速度下测得的铜流失量。
从这个实验中得到的结论是:
1、在接触时间内铜会流失;
2、同其他研究所的结果一样,Sn-Cu-Ni合金造成的铜流失较少;
3、没有明显的迹象表明腐蚀效应比分解效应更明显;
4、发现电路板与电路板之间和不同的供应商之间有比较明显的差别,这不仅仅是因为孔与孔之间的间距,还因为使用了不同的合金;
5、不管在哪一种合金中,长接触时间的焊接工艺都会对通孔转角处( knee dimension)有显著影响,因此在工艺设计的过程中需要考虑这一因素。非常不幸,为了获得理想的工艺流程需要量化数据,这些数据又依赖于截面的显微分析,但是不同批次的电路板和不同的供应商之间存在的铜厚的差异是此次研究完全无法控制的一个变量。
现场经验
从使用隧道式扩展双波峰焊系统用户的反馈来看,结果是积极的。在一面上,缺陷率从47dpm下降到25dpm,下降了47%。这个产品是大尺寸厚服务器电路板。通孔填充率有了改善,焊锡空洞消除了。此外,氧化残留物(锡渣)从1.4公斤/小时下降到30克/小时,同时保养间隔时间由8小时增加到了72小时。图11为三种系统的残留物目视比较,在空气中(右),焊接界面层(中),隧道式(左)。
结论
在波峰焊喷嘴设计中存在着各种各样的变化,每一种设计都有各自的优势和不足。在这些系统中波峰接触时间的差异也是非常大的,这才是提供良好焊点质量的关键因素。工艺工程师应该先考虑需要焊接的电路板然后再来选择最合适的喷嘴。

图11:残留物比较
无铅焊接对波峰焊不断地提出新的工艺挑战。当使用目前标准的喷嘴进行焊接时,对于有大的接地层的复杂的厚的电路板会遇到很大的困难。但是使用扩展型喷嘴时将会克服这些困难,并且可以提供更好的合格率,更低的运作成本,以及更可靠的产品。