清洗工艺的效果
研究表明,选择一种适合的清洗工艺会带来以下改善:
● 键合能量减小 → 减少跟部断裂的风险
● 拉力/剪切力增大 → 键合可靠性增加
● 标准差减小 → 质量稳定/一致性提高
优化清洗工艺后,键合能量和时间可大幅减少,从而使引线键合更具可靠性。过度键合造成的引线变形的风险以及随之而来的跟部断裂都将显著降低。用不含表面活性剂的微相(MPC)技术清洗的键合部分所要求的超声功率比未经处理的新零件还要低(见图5)。作为一个积极的副作用,代工部件的质量波动可以得到一定的补偿。
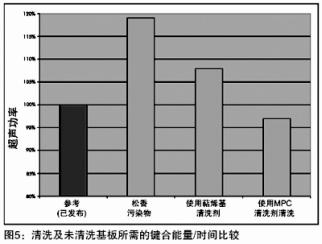
此外,运用了基于MPC?技术的清洗工艺后,拉力与剪切力大大增强,键合质量也相应提高,键合点剥离的风险也随之降低。此外,拉力与剪切力的统计显示出标准差减小。整个引线键合工艺更稳定,一致性提高。键合中的不良达到最小化。图6显示了使用传统表面活性清洗剂和微相清洗剂清洗的基板的拉力与剪切力的比较。
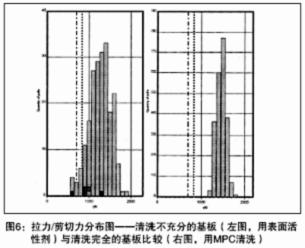
相同数量的部件经过使用两种不同清洗剂清洗测试后发现,使用MPC?技术清洗的部件的拉力要比使用表面活性清洗剂清洗的部件更好。这是由于传统表面活性清洗剂的漂洗能力有限,它会在表面上留下很薄的残留物层。使用传统表面活性清洗剂清洗的表面,其拉力与剪切力会减弱,有时甚至低于规定值。因此,传统表面活性剂产品已不再适用于键合前清洗了。
除了上述优点,优化的清洗方式可使金属基板表面活化,这体现在表面能的增大,同时也对后续工序产生有益的影响。对于后续的灌封和涂敷工艺,表面的附着力提高了。
表面质检的分析方式
Zestron不仅进行如上所述的清洗与键合的试验,还通过研究开发出一系列简单迅速的质检分析方法。这些方法可以直接运用于生产过程中进行工艺监控。
通常,键合工艺通过记录键合时间和能量,观察引线变形来进行监控,并将这些数据与以前的经验结果进行比较。此外,破坏性的拉力与剪切力测试也被用来评估键合质量。在键合工艺前进行非破坏性的表面键合力测试的方法直到现在仍被忽视。
根据Zestron的研究,推荐以下几种在引线键合前进行表面质检的方法:
● 通过干涉对比来验证键合焊盘的表面镀层是否完好
● 通过 ZESTRON树脂测试判定是否存在树脂/松脂
● 测量表面张力
● 通过ZESTRON有机层测试论证表面活性
使用干涉对比法可得知键合点上的金属镀层是否完好。这项测试可检查出使引线键合发生困难的氧化层(见图7)和结构误差。