Stefan Strixner —ZESTRON 欧洲高级工艺师
表面的污物常常会影响引线键合的质量,将合格的质检方法和有效的清洗工序相结合,可以保证工艺的可靠性和可重复性。
作为电子组装件生产工艺中的一部分,引线键合技术是一项超声摩擦焊接工艺,使芯片与各自的基板表面建立电连接。例如在COB(芯片直接粘接)技术中使用细金线,或在高功率模块生产中使用粗铝线。如果考虑低成本制造,也可以使用铜线。
引线键合的常见问题
各种不同工艺都存在共同的缺点——表面杂质。例如,焊接工艺中产生的助焊剂残留或氧化层会降低键合的质量及长期可靠性。这类污物层会直接导致拉力和剪切力的减弱,如果键合能量不够会导致引线连接力不够,其表现为焊接部位剥离(见图1)。
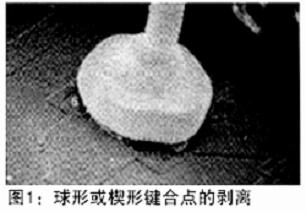
新型的键合设备可通过自动延长键合时间和增加键合能量,使已受污染的表面以摩擦力键合,形成足够大的粘结力;然而,这在很大程度上这会引起引线变形,还会频繁引发键合点跟部的引线断裂(见图2)。
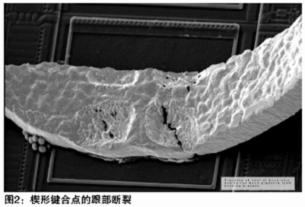
总体而言,键合的时间、能量不同都会对一致性产生不良影响,并且波动范围大(标准差大)。此外,在后续的化合物灌封时,助焊剂残留会导致附着力降低。此外,还会发现引线与芯片的腐蚀问题(见图3),这也是由残留物造成的。此类问题会降低组件或器件的长期可靠性。
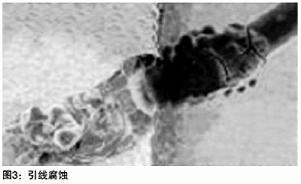
采用清洗改善引线键合质量
鉴于上文提到的情况,通常会在引线键合前进行清洗以改善键合质量,这样能在获得良好的键合附着力与把引线变形的可能降到最低之间取得平衡。因此,应用一项符合引线键合工艺要求的清洗工艺是十分重要的。清洗工艺必须能够去除焊盘上的杂质并且不能在表面上留下任何残留物。
为了找出不同清洗工艺对引线键合工艺的影响,Zestron做了大量的研究。主要做法是,把引线键合到不同表面处理的基板上,并用F&K Delvotec手动焊线机(见图4)进行焊接,用Delvotec的设备进行拉力与剪切力测试。
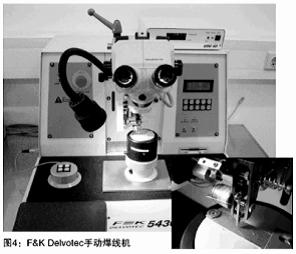
为了对行业内最常用的几种不同清洗方法进行典型化对比,对最常用的参数进行了不同的设置,因而本次测试使用最常见的金属表面处理方式,所研究的污染物代表了由最常用的助焊剂和焊接系统所产生的最为常见的污染物。此外,两项被测试的清洗方式代表了市场上95%的清洗应用。
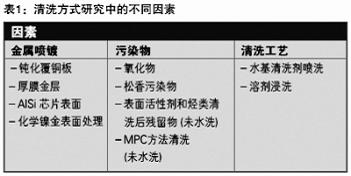