1、引言
传统的开关电源采用模拟控制技术,使用比较器、误差放大器和模拟电源管理芯片等元器件来调整电源输出电压,存在着控制电路复杂、元器件数量多以及控制电路成型后很难修改等缺点,不利于开关电源的集成化和小型化。近年来随着微电子学的迅速发展,电源的控制也已经由模拟控制、模数混合控制,进入到数字控制阶段,具有可编程性、设计可延续性、元件数量减少、先进的校正能力等优点。以往由于DSP等控制芯片的高成本,数字控制多用于大功率AC/DC 变换器、PFC功率因数校正等场合,而对于DC/DC高频开关电源只是实现了一些数字化的简单应用,如采用MCU提供保护、监控和通信功能。随着数字控制芯片成本的降低,数字控制也逐渐应用于DC/DC直流变换器,直接参与电源的反馈回路控制,实现了信号采样补偿和PWM调节的数字化。数字PID补偿器的设计非常关键,直接决定了电源的输出精度、动态响应等指标。近年来对DC/DC 开关电源的数字补偿器的建模研究已有很多论述,主要基于数字重设计法和直接数字设计法。数字重设计是在传统模拟电源研究方法的基础上,首先将数字电源简化为一个连续的线性系统,忽略了采样保持器效应后设计模拟补偿器,然后采用双线性近似(Tustin)、匹配零极点(MPZ)等方法对其离散化得到数字补偿器。直接数字设计是直接建立零阶保持器和被控对象的离散模型,再构建包括离散补偿器的反馈系统。数字重设计和直接数字设计法在高采样速率下设计的数字补偿器性能差别不是很大,只是在低采样速率下直接数字设计更加精确。尽管基于数字重设计法构建补偿器已有相关论述,但其补偿器的设计大都忽略了数字采样系统的延迟效应,从而没有考虑到采样速率对系统设计的影响,产生了一定的误差。
在数字电源建模过程中引入了采样系统的等效延迟环节,基于Matlab 的SISO Design Tool 平台,在伯德图分析和根轨迹法的基础上设计了模拟补偿器并离散化。数字补偿器的设计是在给定的系统采样速率下完成,考虑了数字控制系统固有延迟特性对系统的影响,从而改善了数字重设计法的误差,实现了PWM调节的精确控制。仿真结果证明了理论分析的正确性。
2、数字电源S域建模
数字电源的主功率回路和模拟电源一样,完成输入电压的隔离变换;而信号反馈回路实现了数字化,应用AD、DSP 等数字芯片完成电压反馈信号的数字化处理和数字脉宽调制输出(DPWM)。图1 给出了以DSP 芯片TMS320C2000 为核心控制器的DC/DC 开关电源结构框图。功率回路采用隔离式正激变换器拓扑结构,输入电压信号在功率开关管Q的作用下,通过变压器T 传输到次级,经整流管D和输出电感电容滤波后,输出给负载RL。控制电路对输出电压和输入电流信号采样,采样信号经信号调理电路滤波放大后输入到DSP 控制芯片的ADC 模块,CPU中枢对得到的数字信号分析处理,根据程序设定的算法完成PID校正并输出PWM驱动方波,改变功率开关管的导通占空比以调节输出电压,而形成闭环控制回路。
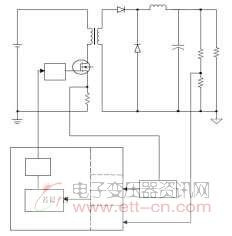
图1 数字控制DC/DC正激变换器结构图
从图1 可以看出数字电源和模拟电源最关键的区别在于控制环路的实现方式不同。模拟电源的反馈控制回路主要由模拟芯片组成,输出反馈电压送入误差放大器产生误差信号,经PID校正补偿后输入到PWM电源管理芯片,产生PWM驱动信号。PID补偿控制算法由运放、电阻、电容等搭建的模拟电路实现,而PWM电源管理芯片也是模拟集成电路,通过比较输入电压信号和三角波振荡信号来输出驱动方波。数字电源的控制回路则完全实现了数字化,反馈电压信号经AD转换为数字信号后,一切都是数字化处理,通过DSP 芯片的内置程序完成PID补偿校正和PWM信号调节,即数字PID补偿器和DPWM模块。
传统的数字重设计法通常忽略了零阶保持器的滞后效应,先在S域设计一个模拟补偿器,然后进行模拟补偿器的离散化。这样处理没有考虑采样速率的不同对系统的影响,产生了设计误差。为了改善离散设计,在建立闭环系统s 域小信号模型时,引入了数字控制回路固有的延迟效应。在受控对象的原始模型中插入延迟环节可以分析采样速率对系统的影响,减小数字重设计法的误差。
为了构建数字电源在S域的系统框图模型并计算其传递函数,根据图1 的电路框图可以将电源整个闭环回路分为几个主要部分:功率级电路Gp(s)、信号调理和ADC采样Gad(s)、数字补偿器GC(s)、延迟环节Gdl(s)和DPWM发生器Gdpwm(s),整体框图见图2。
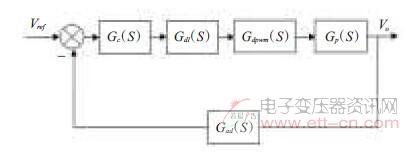
图2 数字电源在S域的闭环结构图
功率级电路完成输入至输出大电流信号的隔离变换,其传递函数时可以看作PWM占空比d 到输出电压Vo之间的转换关系。如果考虑到输出滤波电容的串联等效阻抗Re,得到的传递函数如下:
Gp(s) =(Recs + 1)/(LC((Re + RL)/RL)S2 +(L/RL+ Rec)s + 1) (1)
数字电源控制回路里的延迟效应是由数字芯片的工作特性所决定的,主要由AD转换器和DPWM发生器产生。ADC接收模拟信号后,由主程序控制进行AD转换,转换完成后调用中断处理程序输出数字信号,其延迟时间Tad包括AD转换时间和处理器中断延迟时间;DPWM发生器在输入数字占空比信号到输出模拟PWM驱动信号之间的转换也存在一定的延迟时间Tdpwm。将控制回路里主要的延迟效应用一个延迟环节来描述,等效延迟时间为Td=Tad+Tdpwm,则传递函数为:
Gdl(s) = e-sTd (2)
延迟时间Td与采样周期Ts存在着一定的比例关系,延迟环节的引入在设计模拟补偿器时可以分析采样速率对系统的影响。为了方便构建闭环系统的s 域传递函数模型并应用Matlab 程序计算分析,对延迟环节的传递函数进行Pade 近似处理,得到的延迟环节函数(3)可以直接插入到数字电源的原始模型中,针对采样延迟时间Td来调整补偿器以获得良好的响应。
Gdl(s) =(1-sTd/2)/(1+sTd/2) (3)
电源的输出电压和输入电流信号由于幅度匹配的需要,必须经过信号调理电路处理后才能被AD转换器接收。ADC的采样延迟时间已经在延迟环节里考虑,而信号调理电路和AD转换器的电压增益分别为Kv和Kad,则传递函数可以简化为:
Gad(s) = KvKad (4)
DPWM发生器接收到补偿器输出的数字占空比信号后,应用片上定时器模块输出PWM方波驱动主开关管的导通和关断,其在控制回路中的作用类似于一个D/A 转换器。DPWM的分辨率必须高于AD转换器的分辨率,即DPWM的位数npwm必须大于AD转换器的位数。否则DPWM的最低有效位(LSB)调节的输出电压幅度大于AD转换器的LSB 对应的电压分辨率,而导致设定的输出电压处于振荡状态,即所谓的“极限环”状态。因为延迟时间已经归一到延迟环节里,传递函数可以简化为:
Gdpwm(s) =Kdpwm=1/(2ndpwm–1) (5)
3、数字补偿器设计
通过上述分析,获得了图1 所示数字电源在s 域的传递函数模型,下面基于系统要求的稳态和动态性能来设计数字补偿器。采用的系统参数如下:输入电压Vin=36~72 V,输出电压Vout=5 V,输出电流Iout=6 A,PWM频率fpwm=300 kHz,L=8 μH,C=200 μF;要求动态恢复时间ts<200 μs,相位裕度PM=45 ℃ 。
应用了Matlab 程序的“Sisotool”工具箱进行系统s 域模拟补偿器的计算机辅助设计。“Sisotool”模块是Matlab 控制系统工具箱提供的一个强大的单输入单输出线性系统设计器,为用户提供了很友好的图形界面。应用“Sisotool”工具可以很方便地进行系统的频域分析和补偿设计,在根轨迹法和伯德图法的基础上通过修改线性系统的零点、极点以及增益等进行模拟补偿器的设计,以获得所需要的稳态和动态性能。
为了减小传统数字重设计法的误差,在建模闭环系统时引入了等效延迟环节,补偿器的设计结果和采样速率密切相关。采样速率的确定取决于DSP 芯片TMS320C2000 设置的数字采样方案。在定时器输出的PWM脉冲中间时刻设置了AD转换触发,转换完成后设置新的PWM占空比数值,在下一个PWM周期开始时生效。因此,采样周期Ts和PWM开关周期相等,计算得到的延迟时间Td=Ts/2。
将Td=1.665 μs,Re=0.64 Ω,RL=0.83 Ω等系统参数代入公式(1)和(3)中,并将DPWM发生器和AD采样的比例系数归一化,得开环传递函数:
GOL(s) = Gdl(s)×Gdpwm(s)×Gp(s)×Gad(s) =((1.28×10-4s + 1)/(2.83×10-9s2 + 1.376×10-4s + 1))·((1 - 0.833×10-6s)/(1 + 0.833×10-6s)) (6)
在MATLAB中建立系统开环模型GOL(s)后,将该模型导入到“sisotool”设计工具箱,得到未添加补偿器的开环系统伯德图和根轨迹图,见图3。
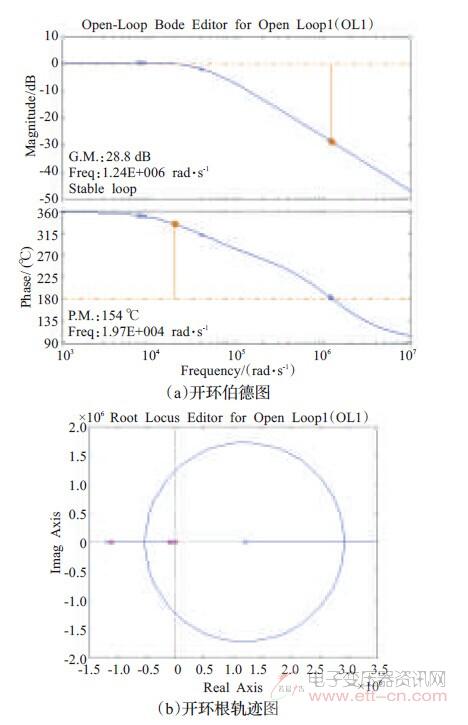
图3 系统开环伯德图和根轨迹图
由图3 看出开环系统的相位裕度不符合设计要求,而且根据延迟环节的传递函数(3),采样周期Ts引入了一个RHP 零点,会导致系统动态响应迟缓。因此,为了补偿RHP 零点并调整系统的相位裕度,必须添加PID补偿器。应用“Sisotool”工具栏可以很方便地重复配置补偿器的零极点和增益,以得到理想的时域和频域特性。最终确定的补偿器的传递函数为:
Gc(s) = 2.4215·105·((1+7.2×10-7s)·(1+5.7×10-6s)/(s·(1 + 4.1×10-7s))) (7)
加入补偿器后的开环系统伯德图如图4 所示。在补偿器控制下,系统的相位裕度为43.8 ℃ ,符合设计要求。
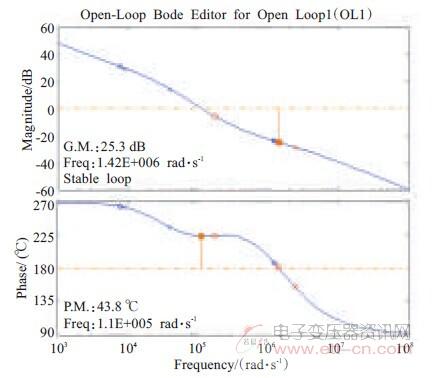
图4 带补偿器的系统开环伯德图
得到模拟补偿器Gc(s)的传递函数模型后,可采用Tustin变换、零极点匹配等方法进行离散化。采用了Tustin 变换法,即双线性变换法。其通过S域到Z域变量准确的映射关系来得到离散传递函数,可以准确地逼近原模拟补偿器的性能。应用MATLAB 仿真软件可以快速地实现Tustin 变换,得数字补偿器G(cz):

数字补偿器以差分方程的形式可以写成:
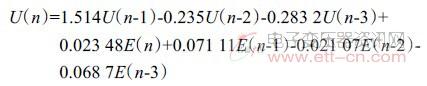
其中,U是补偿器输出的控制电压,E是误差电压。带(n)的参数表示当前采样周期的数值,带(n-1)的参数表示上一个采样周期的数值,以此类推。公式(9)即为数字补偿器的控制算法,通过TMS320C2000 的程序实现。控制算法中的参数是在一定的采样速率下得到的,即设计结果考虑了数字控制的固有特性对系统的影响,从而减小了传统数字重设计法的误差,完成了对PWM驱动调节的可编程精确控制。
4、仿真实验结果
为了验证数字补偿器的性能,对数字电源闭环系统进行仿真分析,仿真电路参数设置同上。图5 为引入数字补偿器的闭环系统阶跃响应曲线。由仿真分析结果可见,系统具有良好的动态响应,调节时间为80 μs,满足系统设计的动态参数要求;超调量得到改善,稳态误差限制在1%以内,实现了系统高精度电压的稳定输出。由数字补偿器校正后的电源闭环系统稳态和动态性能参数符合实际的设计参数要求,从而验证了数字补偿器理论分析和设计方法的有效性。
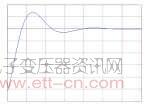
图5 带补偿器的闭环系统阶跃响应
5、结论
基于数字重设计法针对正激DC/DC 变换器设计了数字补偿器。对数字控制正激变换器系统的各个组成模块分别在S域建模,在伯德图分析和根轨迹法的基础上设计了模拟补偿器,然后采用Tustin 变换法进行离散化得到数字补偿器。数字补偿器的设计引入了数字采样校正环路固有的延迟效应,设计结果和采样速率密切相关,从而改善了传统数字重设计法的误差,实现了PWM调节的可编程精确控制。仿真实验结果表明,经数字补偿器校正的系统具有良好的稳态和动态特性。
(小编整理。敬请关注微信号:dzbyqzx)