日本汽车制造商本田希望通过智能设计和先进的制造工艺,来提升燃油经济性、减少车辆排放。近日本田研发部与软件公司Autodesk合作,重新设计并3D打印汽车发动机曲柄组件,使其更轻巧更省油。
在汽车发动机中,曲柄起着至关重要的作用,将活塞运动转换成旋转力。为了始终如一地发挥功能,曲柄必须非常坚固且耐磨损。由于这些原因,曲柄的设计多年来一直保持不变,直到现在几乎没有任何设计变更。
本田研发部门的机械和流体学设计师Hirosumi Todaka解释说:“曲柄需要满足多种功能标准。其形状必须能够承受燃烧压力,并且必须保持旋转平衡,这些因素决定了曲柄的形状。在发动机开发的悠久历史中,曲柄设计已成定局。尽管如此,我们设定的挑战性目标是改进曲柄设计从而减重30%。”
本田早就知道使用增材制造和智能设计来优化汽车零部件的好处。迄今为止,该公司已使用该技术重做了一系列部件,包括安全带支架、发动机控制单元和车架,并且成功实现了轻量化。为了给曲柄组件提供新的设计,本田的研发团队与Autodesk合作,结合前者对该零件的要求和后者的生成设计经验,实现融合优势。
Autodesk提出了第一批模型,使用Netfabb和Fusion 360满足了本田对曲柄的要求。像许多生成设计的模型一样,更新后的曲柄具有有机结构,与传统的曲柄非常不同,甚至超出了汽车工程师的想象。
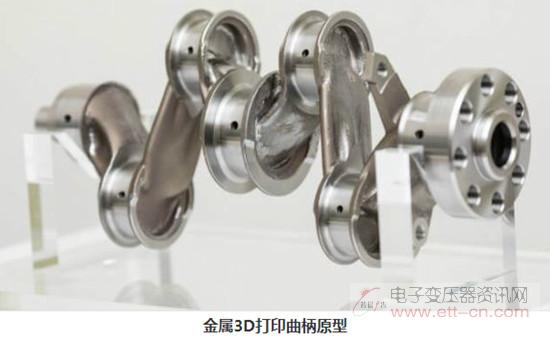
因此,本田派出了一个团队前往英格兰的Autodesk技术中心,接受了生成性设计培训并探索3D打印的更多潜力。重要的是,在Autodesk工厂,本田汽车工程师能够评估3D打印的原型,并根据新的边界条件进一步调整曲柄设计,并开发了第二批模型。
新的部件重量减轻了50%,与本田研发团队使用传统工艺所制造的曲柄完全不同。不过还需要进行测试以确保零件的性能与传统曲柄一样好。Autodesk现在正在使用性能测试中收集的数据,来进一步完善零件及其生成设计过程。
Todaka总结道:“尽管有些人对这种新设计仍然持保留态度,但已经收获了大量关注。将来我希望使用生成设计创建的创新产品将成为常态。我们有责任研究该技术的进一步应用,从而使汽车产业的设计和效率都达到全新的高度。”
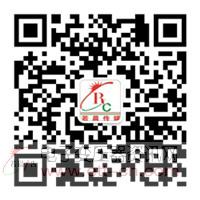
(敬请关注微信订阅号:dzbyqzx)