多孔石墨烯是指在二维基面上具有纳米级孔隙的碳材料,多孔石墨烯不仅保留了石墨烯优良的性质,而且相比惰性的石墨烯表面,孔的存在促进了物质运输效率的提高,特别是原子级别的孔可以起到筛分不同尺寸的离子/分子的作用。
尽管石墨烯在储能领域展现出广阔的应用前景,然而由于在电极制备过程中石墨烯片层的堆叠导致缓慢的离子传输动力学以及下降的活性表面积,严重阻碍其实际应用。基于此,在石墨烯片层上造孔成为一种有效的方法,使多孔石墨烯材料具备石墨烯和多孔材料双重优势。
国家纳米科学中心的韩宝航研究员课题组长期从事有机多孔材料和石墨烯基多孔材料的制备及其在能源储存与转化、气体吸附与分离、催化等方面的应用研究。近日,韩宝航研究员应邀在英国皇家化学会(RSC)期刊Journal ofMaterials Chemistry A上发表题为“Advanced porous graphene materials:from in-plane pore generation to energy storage applications”(https://doi.org/10.1039/D0TA00154F)的综述文章,详细介绍了多孔石墨烯材料的面内造孔方法以及面内多孔石墨烯基材料在储能器件中的研究进展。此外,还总结了这类材料在实际应用中的挑战并展望了该面内造孔方法对其它二维材料的启发。
目前,制备面内多孔石墨烯材料的方法可以分为有机合成法、模板导向法、物理蚀刻法和化学蚀刻法。通过使用不同的制备技术,石墨烯片层上面内孔的孔径范围可以从原子尺度到纳米尺度。
有机合成法是一种自下向上制备面内多孔石墨烯材料的方法。为了制备高质量的面内多孔石墨烯,需要选择合适的刚性分子构建块作为前驱体。图1为通过自下而上的有机合成法制备纳米多孔石墨烯的示意图。该刚性前驱体先脱溴然后经过偶联反应聚合生成聚合物链。合成的聚合物链可以通过分子内环脱氢形成平面石墨烯纳米带。最后,通过这些石墨烯纳米带的脱氢交叉耦合,制备出孔径约为1 nm的多孔石墨烯。
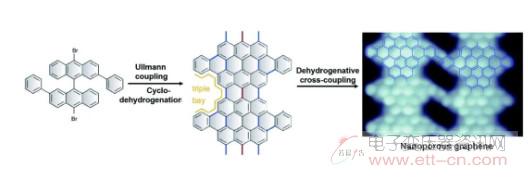
图1. 通过有机合成法制备纳米多孔石墨烯的示意图
模板导向法是一种通过选择合适的模板以及改变制备参数直接调节片层上孔径分布和孔密度的方法。图2以单分散胶体微球作为模板,采用反应离子刻蚀工艺构造胶体微球之间的孔隙。在基底表面上沉积掩模并选择性地去除微球后,得到了具有连续孔的掩膜。进一步改变反应离子蚀刻的持续时间,可以很好地控制掩膜的孔径大小和孔密度。
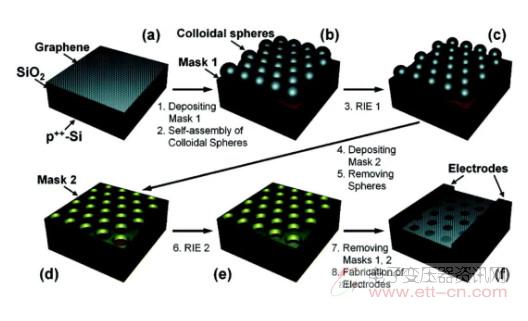
图2. 模板导向法制备面内多孔石墨烯材料的示意图
物理蚀刻法是指利用诸如等离子体、紫外线、激光、离子束和电子束等技术,采用自上而下的方法来制备多孔石墨烯材料的方法。图3a为采用聚焦离子束技术制备多孔石墨烯的工艺过程。制备工艺包括五个步骤: 1) 通过KOH刻蚀获得独立的SiNx膜; 2) 通过光刻和反应离子刻蚀,在SiNx膜上形成多孔结构; 3) 转移石墨烯; 4) 石墨烯表面清理; 5) 通过镓基和氦基的聚焦离子束钻孔技术,在石墨烯平面上形成孔隙。从图3b和3c可以看出,用镓基和氦基的聚焦离子束在石墨烯上分别形成了50和7.6 nm的孔。
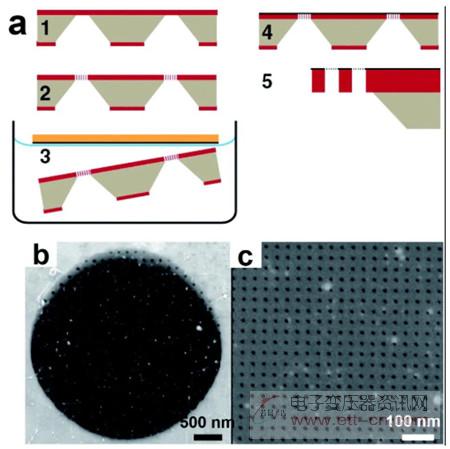
图3. (a) 面内多孔石墨烯的制备工艺; (b和c)面内多孔石墨烯膜的SEM图像。
化学蚀刻法是利用酸、碱、氧化物等化学试剂对石墨烯片层进行化学刻蚀使其产生面内孔的方法。图4a展示了采用多金属氧酸盐衍生的金属氧化物刻蚀,可以得到面内多孔石墨烯材料,石墨烯片层上的孔径约为20–50 nm (图4b)。通过改变多金属氧酸盐的用量,可以控制多孔石墨烯片层上的孔径大小。选择含氨的多金属氧酸盐可以很容易地实现面内多孔石墨烯材料的氮掺杂。