德国政府 2011 年提出了工业 4.0的概念,对全球科学界、产业界和工程界产生很大影响。工业4.0的核心在于通过建构智能化生产流程提高生产效率、速度和灵活性。与工业4.0相对应,中国国务院于2015年5月提出“中国制造2025”的概念。这两个概念关于信息交流技术与制造技术深度融合的观点是一致的。但“2025”也从中国国情出发,强调了实现传统制造业转型升级、高端制造业跨越式发展以及从资源消耗型制造向绿色制造转变的重要性。因此,无论从“工业4.0”还是“中国制造2025”来看,高性能机器人和智能自动化生产线将在未来工业中扮演着非常重要的角色。
根据国际机器人联合会(International Federation of Robotics,IFR)估计,2014 年全球仅工业机器人市场销量就约 22.5 万台,创历史新高。未来市场需求还将持续增长。而服务型机器人也具有很强的发展潜力,IFR 预测其 2014 年至 2017 年市场总销量可望突破 3,100 万台。其中,中国机器人市场需求量预计将占全球总量的五分之一,居全球之首。
为了实现越来越复杂的运动和加工程序,现代工业的发展对机器人和自动化生产线的活动自由度 (Degree of freedom, DOF) 提出越来越高的要求。具有6个DOF的机器人已经被广泛应用。而目前有些自行式Robot的DOF甚至高达25。随着“工业4.0”和“中国制造2025”的实施,机器人的DOF无疑将进一步增加。而每一个DOF都意味着需要一个电机和与之相匹配的驱动控制系统。由此可见,今后机器人和自动化生产线对电机及其驱动系统的要求会越来越高。
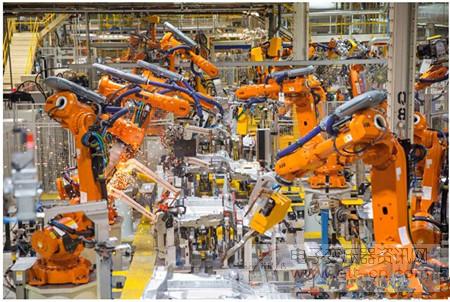
现代机器人对电机的基本要求包括高功率密度、高效率、低震动和低噪音,既有运动控制方面的要求,也有环保方面的要求。在许多应用场合,也需要高转矩密度,比如自行式机器人的手指。高功率密度意味着能够以较小的电机尺寸和重量实现较高的功率运行。高转速电机是实现高功率密度的一个有效并且直接的解决方案。对于需要高转矩密度的场合,可以通过高速电机加微型减速齿轮箱的方案来实现。高转速、低震动、低噪音和高效率的实现,除了对电机本体有较高的要求外,对电机驱动也是一个挑战。
根据目前电机发展趋势,以电磁反应来实现机电能量转换的电机,仍将在现代电机中占主导地位。其中,依赖于高性能永久磁钢的无刷直流电机 (Brushless DC Motor, BLDCM) 和永磁同步电机 (Permanent Magnet Synchronous Motor,PMSM) ,凭借优异的性能和高可靠性,今后将在机器人和智能生产中发挥举足轻重的作用。
BLDCM和PMSM都必须和驱动器结合才能运行。为了充分发挥这两种电机的作用,许多驱动模式应运而生。这些驱动模式都是根据电机的电磁特性发展出来的。例如,对应于三相PMSM,若其三相反电势与转子位置的关系是正弦且对称的,在理论上可以证明,当三相电流与也是正弦且对称的,则电机产生的电磁转矩是恒定的。如果电流的直轴分量为零,则电机的效率为最佳。这就是目前在PMSM上得到越来越广应用的磁场定向控制 (Field Oriented Control, FOC) 的驱动模式。而近来发展较快的“直接转矩控制” (Direct Torque Control, DTC) 驱动模式,则是通过对定子电压和电流的检测, 来计算转矩和磁链的幅值。并且通过控制定子磁链的幅值以及该矢量相对于转子磁链的夹角, 进而达到对磁链和转矩直接控制的目的。这两种驱动模式都需要控制器根据电机的参数、转子位置和控制要求计算出所要求的三相绕组的瞬时电流的值的控制信号,而驱动器的功率半导体器件则必须按照控制器的信号以开关斩波的形式把电源输入到电枢绕组的电压进行脉宽调制(Pulse Width Modulation,PWM),以准确和及时地产生电机绕组所要求的电流。这些对控制器的计算速度和功率器件的开关速度都有很高的要求。可以预测,今后机器人和自动化生产线除了会针对电机的特性提出控制要求外,还会对负载的状况以及环境的变化提出更加复杂的控制要求,进而促使新的电机驱动模式的产生。这些都会对电机控制器和功率半导体器件提出新的挑战。
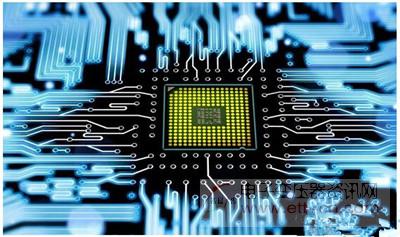