1.卷制采用变频电机与机械六档变速相结合
根据不同宽度的绕线需要不同的输出扭矩这一工艺特点,采用变频电机与机械六档变速相结合的方式,即实现了无级变频调速,又实现了电机功率的合理配置。因为要使大尺寸的绕线绕制紧密,需要的张力大,主轴要求低速大扭矩输出;而要使小尺寸的绕线绕制紧密,需要的张力小,主轴要求高速小扭矩输出。若不用机械变速,输出1000Nm扭矩需要选用40kW的电机;而采用六档机械变速,同样输出1000Nm扭矩只需要选用3kw的电机。因此在国外设备变频调速的基础上采用了六档机械变速与其相结合,即扩大了变速范围(24.5~357r/min),又节省了能源,降低了成本。
国外绕线机设备在电机与主轴间采用同步齿形带传动,我们采用窄V带传动,抗冲击能力强,工作平稳,过载可以打滑,具有安全保护作用。主轴制动采用摩擦制动器制动,安全可靠。绕制速度的选择通过主轴箱上的换挡手柄完成,十分方便。
2.采用编码器和可编程控制器控制步进电机来实现任意宽度绕线自动排线我们在排线系统中通过装在全自动绕线机主机主轴上的编码器发出信号,经过可编程控制器计算,由步进电机根据接收的信号驱动排线架移动,来实现任意宽度绕线的自动排线。如此高的排线精度(±0.005mm)靠普通的丝杠传动是无法实现的,我们采用高精度滚珠丝杠付,并用双螺母垫片式预紧方式来消除双向间隙,提高轴向刚度,保证传动精度。自动排线和排线精度的解决,确保了排线紧密,缩小了线圈轴向尺寸,免除了人工敲打、整形等操作,并可节省材料,提高绕制效率和线圈质量,增强变压器抗突发短路能力。
3.尾座移动采用齿轮齿条机构
国外设备的尾座移动采用棘轮机构,绕线机主机尾座采用齿轮齿条机构,即可手动调节尾座移动,又可自动调节尾座移动。
4.放线架采用机械张紧
国外设备的放线架上装有气动盘式摩擦阻尼器来形成张力。我们采用弹簧调节放线架上张紧轮摩擦力,实现绕线的张力调整,减小线圈径向尺寸,保证线圈质量。
5.绕制线圈的匝数采用电子计数
采用编码器实现线圈匝数的自动计数,计数准确、方便。
6.采用可编程控制器进行控制和数据处理
全自动绕线机
采用可编程控制器实现系统控制和数据处理,最大限度地缩短了选定绕线宽度(或直径)和理想停车圈数的设定时间。操作者只需输入绕线宽度(或直径)和停车圈数,可编程控制器便可根据设定的线宽计算主轴转一圈步进电机应走的步数,并根据设定的总匝数控制主电机和步进电机的停止,增强了系统可靠性。
原有绕线设备存在的问题:
1.卷绕采用异步交流电机驱动,启动、制动不平稳,线圈在绕制过程中由于启动、制动频繁,使得线圈松紧程度不均匀,张力不均衡;
2.排线和张紧均采用人工操作,在绕制过程中需要不断敲打、整形,由此绕制出来的线圈径向和轴向尺寸必然偏大,导致变压器铁心窗口尺寸和油箱尺寸随之加大,最终导致变压器生产用料增多、成本提高,变压器重量和体积增加;
3.由于每个人在绕制线圈时用力不同,致使绕制的线圈松紧程度不同,变压器三相平衡差,从而影响了变压器的质量。
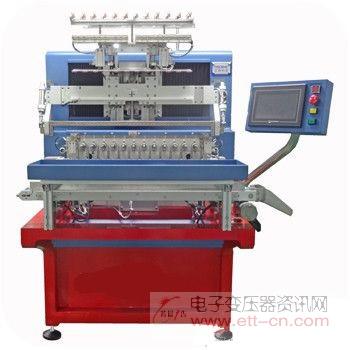
改进后的绕线机的现状:
通过查阅有关国内绕线机现状的资料,及深入到生产第一线调查现有绕线机存在的问题,认为国内绕线设备总体相对落后,难以满足新产品的工艺要求,主要表现存以下几个方面:
1.卷绕采用异步交流电机驱动,绕线机启动、制动不平稳,线圈绕制不紧;
2.排线和张紧采用人力手工操作,排线不均匀,无法实现恒张力,劳动强度大;
3.设备自动化程度低,计数器可靠性差。
国外绕线机的特点:
国外高压线圈绕线机主传动采用变频电机通过同步齿形带直接带动绕线机主轴及花盘转动,绕线模由主轴顶尖和尾座顶尖定位,绕线模一端与花盘连接传递动力。尾座的移动采用棘轮机构。采用步进电机通过滚珠丝杠带动排线架移动来实现排线功能。排线架移动与主轴转动的协调是由计算机控制的。放线架上装有盘式摩擦阻尼器来形成张力。进口绕线机自动化程度高,绕线和排线性能好,但价格比国内原有绕线机高出十几倍。目前国内绕线设备正面临着更新换代,因此变压器全自动绕线机市场需求大,前景广阔。