1、序言
钕-铁-硼磁性材料是将筛选后的钕、铁、硼超细粉历经错料、抑制、煅烧而成的。依据商品主要用途规定,机械加工制造成不一样的样子。因为这类原材料物理性质较为活跃,非常容易被氧化,所以制成品必须开展电镀涂敷生产加工。殊不知电镀涂敷的品质又与它的前处理息息相关。
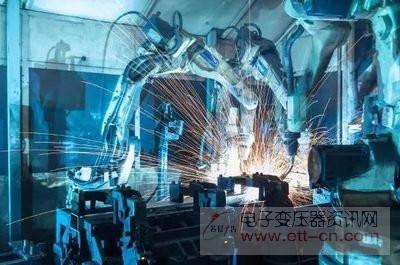
这类前处理工艺一般包含脱油、除铁锈、活性等工艺流程。假如这类前处理方式有一个阶段解决得不干净,都是会给最后的电镀商品造成具有潜伏性的缺点,导致电镀层发生出泡、脱落等难题。
有缺陷的磁性材料零件会丧失销售市场使用价值而损毁。假如含有潜在性缺点的磁性材料零件一旦被运用到机器设备上,或许便会因这类不过关零件上机操作而导致整个机械常见故障,乃至导致严重危害。
2、钕-铁-硼磁性材料电镀前的工艺处理
钕-铁-硼磁性材料并不像铸造金属复合材料那麼高密度。属微孔板型原材料。它的多孔结构给电镀前解决产生诸多困难和不便。除开要除去工件表层上的偏碱、酸性物质和生产过程产生的废弃物外,较大的难度系数是,如何把微孔板中的废弃物消除整洁。
针对一般规定不太高的低档次的磁性材料,过去选用的前处理为:偏碱脱油——水清洗——酸洗钝化(漂白剂、中合)——水清洗——表层活性——电镀。这类加工工艺全过程虽简易,但它对除油剂的规定较高,必须用钕-铁-硼专用型除油剂,这类除油剂的秘方繁杂,必须的原材料类型多,客户配置全过程十分不便。并且一旦配制不合理,便会无效,应用性较弱。
选用超声波清理后,钕-铁-硼磁性材料的前工艺处理一般为:
(1)偏碱脱油——水冲洗——水冲洗——超声波精漂——稀硝酸解决(中合、漂白剂)——水浸洗——水浸洗——超声波精漂——活性解决——电镀。
(2)偏碱脱油——水浸洗——水浸洗——超声波精漂——稀硝酸(中合、漂白剂)解决——水浸洗——水浸洗——超声波精漂——活性解决——水浸洗——水浸洗——超声波精漂——电镀。
(3)超声波偏碱脱油——水浸洗——水浸洗——超声波精漂——稀硝酸(中合、漂白剂)解决——水浸洗——水浸洗——超声波精漂——活性解决——水浸洗——水浸洗——超声波精漂——电镀。
剖析之上三种加工工艺,其不同之处取决于:加工工艺(1)的特性是:活性解决后立即电镀。而(2)(3)二种加工工艺却在活性解决后又进一步应用了超声波精浸洗。应用第一种加工工艺的原因是觉得历经活性解决后的磁性材料工件的表层情况最好,很合适与电镀层融合。非常容易确保电镀品质。而应用(2)、(3)二种加工工艺的原因是觉得活化液偏酸,工件微孔板中的残余酸性物质务必用超声波清理进一步除去才可以确保电镀层品质。这种加工工艺的相同点全是在偏碱清理和酸碱性清理以后选用超声波精浸洗,加工工艺(3)应用了高达三道的超声波清理。
大家强烈推荐有标准的公司选用加工工艺(3),特别是在对高品质的磁性材料选用多道超声波清理比较适合,它能非常好地确保电镀产品品质。自然,客户依据自身的实际操作习惯与商品目标挑选不一样的清理加工工艺除外。
3、清理方法的挑选
工件在清理槽体的放置方法与清理品质有非常大的关联,它的放置方法又与工件的尺寸、样子、构造相关。一般来说,工件中间的重合堆积或一次堆积太多都是会危害清理实际效果。
钕-铁-硼磁性材料尽管形状各异,但多归属于中小型零件。能够将它放到涤纶网上,在清理槽体开展摇晃清理,那样有利于工件表层的废弃物掉下来,也有益于含有埋孔工件的收缩水膜毁坏,使埋孔内易造成空化效应。
另一种放置方法是立即将工件摊平在清理槽底版(也就是超声波换能器辐射板)上,使工件承担明显的超声波冲击性。实践经验证明这类立即将工件放到底版上开展清理的方式,清理实际效果最好,高效率最大。
4、功率的挑选
超声波输出做到一定抗压强度时才可以造成空蚀功效。
一般在水中最少的功率应超过0.3W/cm,殊不知功率过大,清理工作能力提升 了,却有可能导致工件表层的机械设备损害或空化浸蚀。功率过小则生产率太低,乃至工件清理品质达不上规定。一般机械加工制造领域用超声波清洗设备,其面功率为0.40~0.80W/cm,体功率为25W/L上下。